- Home
- Services/IndustriesServicesindustries
- About Us
- LocationsStatesAccordion ContentAccordion ContentAccordion ContentAccordion Content
- Job Openings
- Quick Links
- ATS Family
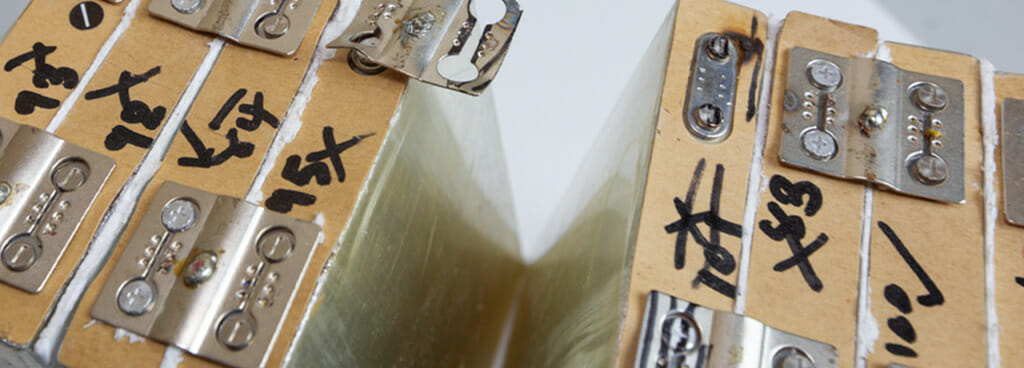
Battery Durability Testing
Battery durability testing with the ATS Family of Companies (FoC) helps manufacturers design reliable products that resist degradation in severe operating conditions. Batteries power critical equipment for long-distance transportation, data storage, and renewable energy generators, all of which require optimal performance and reliability. Durability testing helps manufacturers check that their design holds up to threats such as:
- Corrosion
- Explosion
- Fire
- Hazardous Gas
- Leak
- Loss of Capacity
- Overheating
- Shorter Lifespan
A2LA-Accredited Battery Testing Laboratories
The ATS Family of Companies operates several ISO/IEC 17025-certified labs nationwide. Our experts test battery samples in rigorous conditions that simulate real-life scenarios from regular operation to misuse. To help clients prepare for certification from an NFTL, we can confirm a product complies with national and international standards. ATS follows the electrical and mechanical durability testing procedures outlined in several different standards, including:
- UL 2580
- IEC 12405
- IEC 62660
- SAE J2380
- UN 38.3
Our lab is A2LA accredited in battery testing at the cell, module, and pack levels. Our experts help uncover flaws in design structure, compare options for battery chemistries, and provide insight into battery certification processes. We work with a variety of popular battery chemistries, including:
- Nickel-cadmium
- Lithium-ion
- Lead-acid
Electrical Durability
Electrical durability tests involve subjecting a battery to charging and discharging profiles that simulate various applications and scenarios. Our experts perform a variety of electrical durability tests to study how a battery degrades electrochemically throughout its lifetime, anticipating overcharging, imbalanced charging, and discharging to specific capacity levels.
A more rigorous procedure is Accelerated Life Testing, which pushes the battery to its limits to predict aging and degradation.
Mechanical Durability
Vibration and Shock
ATS FoC experts perform vibration tests that imitate the frequencies produced during transport and operation to evaluate how shock and vibration affect a battery’s mechanical integrity.
Impact and Compression
Our experts subject a battery sample to horizontal and vertical forces to simulate contact with surrounding components during heavy operation or vehicular collision.
Extreme Temperatures
Batteries often need to withstand extreme temperatures for long periods. We perform tests in temperature-controlled environments from -68 ˚C to 190 ˚C and precondition specimens in a water bath of 5 ˚C to 90 ˚C. To ensure safe testing with high temperatures, our experts conduct high-risk tests in a specially designed Hazard Containment Room (HCR) built to counter potential adverse reactions.
A Qualified Testing Firm
ATS is a consulting engineering, calibration, inspection, and testing company with over 55 years of operation. We maintain several ISO/IEC 17025 labs accredited in electrical, chemical, mechanical, and nondestructive testing and calibrations. Our Marietta, Georgia, headquarters includes an FAA repair station and CPSC-approved lab.
Our Family of Companies is a united collection of firms with a broad range of capabilities and expertise. Together, we support industries such as aerospace, automotive, power generation, and renewable energy. Our wide set of skills helps the ATS FoC do more in-house so clients can reach business milestones faster and cost-effectively.
Contact Us
Schedule a battery durability test today by calling +1 (888) 287-5227 or provide your information on the request form on this page.
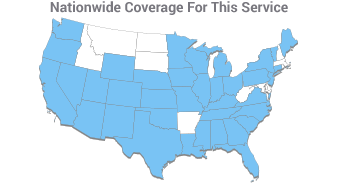
Request Form
"*" indicates required fields
Battery Testing Links
- Abuse Testing Lithium Ion Batteries
- Battery Abuse Testing
- Battery Chemical Analysis
- Battery Durability Testing
- Battery Electrical Testing
- Battery Impact Testing
- Battery Management Systems BMS Testing and Certification
- Battery Performance Testing
- Battery Safety and Certification Testing
- Battery UL Certification
- Battery Vibration Testing
- Chemical Testing EV Batteries
- Electrical Testing EV Batteries
- Electrical Vehicle Battery Testing
- E Mobility Battery Testing
- Energy Storage System ESS Testing and Certification
- E Scooter Battery Testing
- EV Battery Testing Lab
- EV Battery Mechanical Testing
- EV Battery Pack Vibration
- EV Battery Thermal Testing
- High and Low Temperature Testing EV Battery
- Hoverboard Battery Testing
- IEC 60896-21 Stationary Valve-Regulated Lead-Acid Batteries
- IEC 61427 Secondary Cells and Batteries for Photovoltaic Energy Systems Testing
- IEC 62133 Lithium Battery Safety Testing and Certification
- IEC 62133-2 Lithium Ion Battery Testing Certification
- IEC 62619 Secondary Cells and Batteries Containing Alkaline Testing
- Lead Acid Battery Testing
- Mechanical Testing EV Batteries
- Micro Mobility Battery Testing
- PNNL 22010 ESS Performance Testing
- RESS Safety and Abuse Testing
- RTCA/DO-311 Performance Testing Lithium Batteries
- SAE J1798 Performance Rating of EV Battery Modules Testing
- SAE J2185 Life Testing Heavy-Duty Storage Batteries
- Telcordia GR Battery Testing
- Thermal Testing EV Batteries
- UL 1642
- UL Battery Certification
- UL 1973 Battery Testing
- UL 1989 Standby Battery Testing and Certification
- UL 2054
- UL 2271 E Bike Battery Testing and Certification
- UL 2580 Electric Vehicle Battery Testing and Certification
- UL 9540A
- UL 9540 Thermal Runaway In ESS Testing and Certification
- UN 38.3 Testing
- USABC Battery Testing
- Verizon VZ.TPR Battery Testing