- Home
- Services/IndustriesServicesindustries
- About Us
- LocationsStatesAccordion ContentAccordion ContentAccordion ContentAccordion Content
- Job Openings
- Quick Links
- ATS Family
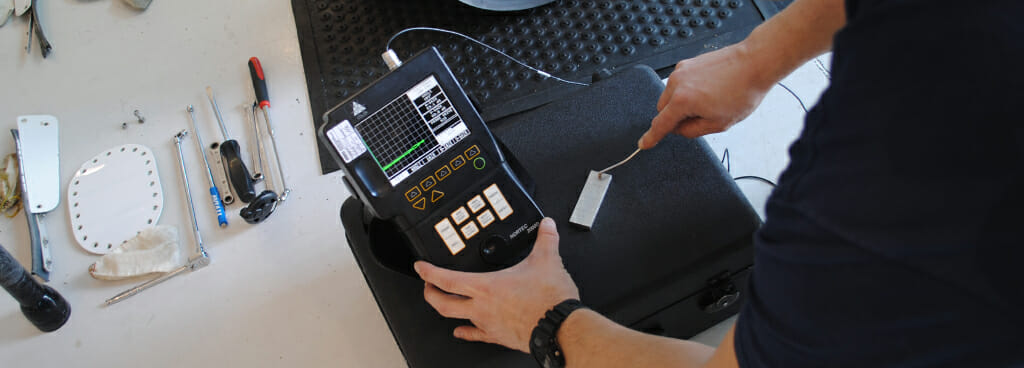
ATS Aircraft Eddy Current Inspection
Applied Technical Services offers aircraft eddy current inspection services for the aviation industry. Our state-of-the-art eddy current testing equipment enables us to inspect aircraft components for irregularities such as cracks, corrosion, and fatigue. Early detection of such defects is important for flight safety and prolonging the life of the aircraft.
Eddy Current Testing — Taking Advantage of Electromagnetic Induction
Eddy current testing (ECT) is a method of nondestructive testing mainly used to detect surface flaws in conductive materials – ideal for the relatively thin metal material found in aircraft. ECT combines electricity and magnetism to create a magnetic field on the conductive metal surface. Our expert ECT technicians look for variations in electrical conductivity readings of this magnetic field, which typically indicate an irregularity on the surface.
Why Planes?
The general flexibility and accuracy of the eddy current testing method make it very effective for nondestructive testing of aircraft components. ETC allows our technicians to scan large areas of the aircraft surface/subsurface (wings, fuselage, etc.) quickly, as well as tight spaces and complex-shaped surfaces.
Additionally, ECT is not affected by non-conductive layers (paint and sealant), requires minimum part preparation before testing, and does not need direct contact with the part. Other aircraft parts that can be inspected with eddy current include engine blades, propellers, rotors, fasteners, and holes.
Common Eddy Current Inspections for Aircraft
Surface and subsurface inspections
The exterior surface of an aircraft can be subject to strong mechanical and environmental forces during normal operation. A thorough eddy current inspection can reveal small cracks or corrosion that could potentially threaten the integrity of the aircraft.
Rotating bolt hole inspections
Bolt-holes can undergo stress after fastener removal that could cause cracking. Our technicians pass a rotating scanner through the bolt hole and monitor the area for signs of cracking.
Magneto-optic Imaging (MOI)
Used in detecting surface/subsurface cracks and corrosion in metallic aircraft skins.
Conductivity measurements
Used for material/temper verification and detecting heat damaged parts.
ATS and Aircraft Eddy Current Inspections
For over 50 years, we at Applied Technical Services have stayed true to our principles of quality service, quick turnaround times, and helpful customer support. Our NDT technicians are highly trained to perform thorough aircraft testing and deliver accurate reporting. Additionally, ATS holds an FAA Repair Station Certification for performing inspections.
Contact us today if you need an aircraft eddy current inspection – we would be happy to tailor our NDT services to your needs. ATS – We take a closer look!
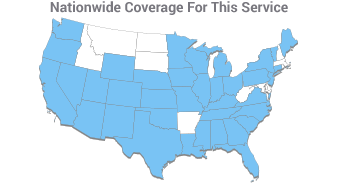
Request Form
"*" indicates required fields