- Home
- Services/IndustriesServicesindustries
- About Us
- LocationsStatesAccordion ContentAccordion ContentAccordion ContentAccordion Content
- Job Openings
- Quick Links
- ATS Family
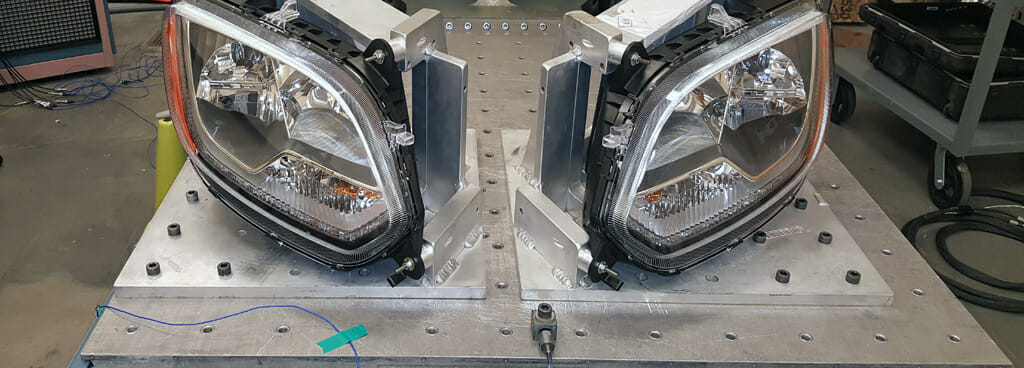
Automotive Vibration Testing
Applied Technical Services performs automotive vibration testing to validate client materials and components for use in production. Automotive products vibrate when in use — no way around it. The motion caused by merely running the engine creates vibrations that propagate throughout the entire assembly, let alone the actual driving. OEMs and automotive engineers understand the importance of ensuring that those vibrations, innate to their product’s intended use, do not damage or otherwise undermine the performance of their components. To validate the performance and durability of materials and components for production, automotive clients send samples to ATS’ trusted vibration testing lab.
Effects of Vibrations on Materials and Subassemblies
Vibrations happen when force is applied to an object. The resulting waves of motion cause the particles of an object to oscillate as the force moves through the material. Different vibrations have different characteristics, varying in amplitude and frequency. Over time, or with enough strength, vibrations can negatively affect materials and components. Subassemblies unsuited for the types of vibration common to the final product’s anticipated service environment can suffer fatigue failures, loosened connectors, interrupted electrical signals, and other negative consequences. Avoiding such defects can mean the difference between a product that meets requirements — whether internal quality assurance measures, industry standards, or government regulations — and a product that endangers end-users because of a susceptibility to premature or unexpected failure.
ATS' Automotive Vibration Testing Capabilities
ATS’ environmental testing division performs all our vibration testing services. These experts use our electrodynamic shaker tables to apply a range of vibrations while precisely controlling their frequency and intensity to create the desired effects. Our advanced instrumentation can apply vibrations with as much as 12,000 pounds of force at any frequency from 5–2,000Hz. Coupling the shakers with AGREE environmental chambers lets us accommodate additional test customization by introducing temperature variations as well.
Depending on the relevant test specifications, we may employ a sinusoidal, random, or sine-on-random vibration regimen.
Sinusoidal Vibration Testing
A sinusoidal vibration scheme only exposes a sample to a single frequency at any given point. They can simulate highly regular vibrational patterns like those generated by the pistons pumping in a running engine.
This method allows our technicians to discover a sample’s resonance frequency by sweeping through a range of frequencies until we find it in a technique called a search and dwell. A resonance frequency is one at which vibrations strengthen as they reverberate through a homogeneous material, causing the amplitudes to grow more than other frequencies because of how each vibration amplifies one another. Also referred to as the natural frequency, this characteristic differs between materials, forcing OEMs to establish their design materials’ resonance frequencies to ensure that they do not overlap with the range of vibrations the final assembly will face in its anticipated service environment.
Our technicians also use sine vibration schemes to age the sample; by applying the material’s resonant vibrations, they can exacerbate any existing minute defects that arose in the production process and cause accelerated fatigue failures. Doing so can help designers understand their products’ prevalent failure modes and work to address them. This method of vibration testing excels in revealing the material’s durability characteristics in idealized circumstances but does not account for the unexpected vibrations.
In contrast, a random vibration scheme exposes a sample to a wide range of frequencies more akin to what it may face in the real world. Technicians apply vibrations at many frequencies to simulate the unpredictable stimuli that will occur in the final assembly’s intended service environment, such as those constant vibrations that the frame experiences while driving over the road.
To perform this type of testing, our technicians first set the range of frequencies and intensities that they will apply to the sample. Choosing the most appropriate test parameters and applying them correctly greatly influences the success or failure of the method. As such, these values are determined by the relevant scope, provided by either a testing standard or client specification. If supplied with data collected and recorded from the actual service environment, our technicians can import the information as a waveform and subject samples to the specific vibrations native to their service conditions.
Random vibration testing offers a more comprehensive understanding of what a given material must withstand to perform effectively in its intended service conditions but does not account for the identical, recurring vibrations that typically come with running machinery.
Sine-On-Random Vibration Testing
The final category of vibration testing, sine-on-random, offers the best features of the other two and synthesizes them. Using this method, our technicians apply a field of random “background noise” vibrations overlaid by a sinusoidal pattern of stronger vibrations. Doing so simulates both the unpredictable and the foreseeable vibrations that a sample must withstand.
Regularly Used Standards and Procedures
The first step to successful vibration testing is securing the sample to the shaker table. We accomplish this by using mechanical fixtures, customized to fit the sample. With a fully equipped machine shop, ATS has the ability to fabricate fixtures in-house, driving down the cost of testing as compared to other labs providing the same service. Our technicians ensure that the fixtures are appropriate to the scope of testing beyond the fit by verifying that their resonant frequencies do not lie within the parameters of the test.
The ATS environmental testing division regularly conducts automotive vibration testing to a variety of OEM standards, as well as the following industry standards for which we maintain ISO 17025 accreditation to perform through the A2LA:
About ATS
Applied Technical Services takes great pride in offering testing, inspection, and consulting engineering capabilities of exceptional quality. We have grown exponentially since our founding in 1967 due to the hard work of our dedicated employees. Over the 50+ intervening years, ATS has gone from a group of three engineers contracting with local businesses out of the founder’s basement to a multidisciplinary service provider. We work to meet the needs of clients operating in countries across the globe through the efforts of over 1,000 technicians, calibrators, chemists, inspectors, scientists, Professional Engineers, trainers, and investigators. While many industries benefit from our broad scope of environmental testing capabilities, our capacity as an automotive vibration testing provider exclusively serves OEMs and parts suppliers.
Our Commitment to Quality
We perform our vibration testing services under the scope of our ISO 9001-registered quality assurance program. ATS initially achieved this certification in 1998 by submitting our business processes to audit by ISO-approved inspectors who determined that our system complied with the internationally recognized standard on effective quality management practices. We have maintained registered status without interruption since then by periodically undergoing this same process for recertification. Our company participates in this exacting process because we want to hold ourselves publicly accountable for the quality of our work. Abiding by the principles outlined in this standard has given us a platform from which we have continually improved both the quality and scope of our services.
To ensure our clients enjoy the best customer service we can provide, we uphold the following policies:
- Testing specialists return clear, accurate, and detailed reporting. Doing so in a quick turnaround window empowers our clients to make informed, timely decisions regarding their sample.
- When clients reach out for clarification on the status or results of their testing, our customer service representatives facilitate contact with the most relevant staff member to help resolve their issue.
- Lab personnel remain accessible to clients with questions, responsive to the needs they express, and engaged in helping them solve their problems.
If your company needs trusted automotive vibration testing services, contact ATS today for a free quote — We take a closer look!
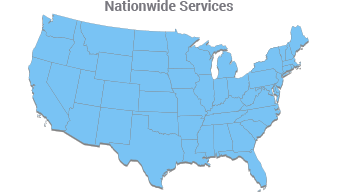
Request Form
"*" indicates required fields
Automotive Testing Links
- Automotive Interior Testing Lab
- Automotive Paint Salt Spray Testing
- Automotive Testing Companies
- Automotive Testing Services
- Automotive TL Testing
- Automotive Vibration Testing
- VOC Testing
- BMW Approved Test Lab
- BMW Approved Testing Lab
- BMW Standards Testing
- BMW VOC Testing
- BO 131 03 Ford Interior Odor Test
- Chrysler Standards Testing
- DIN 75200 Testing
- DIN 75201
- DIN 75220
- Engine Vibration Testing
- Exterior Paint Testing
- Florida Exposure Testing
- FMVSS 302 Testing
- Ford Standards Testing
- Ford VOC Testing
- GM Standards Testing
- GS 97014-3 Testing
- Honda Parts Testing
- Honda VOC Testing
- Honda Standards Testing
- Kalahari Testing
- Mercedes Approved Testing Lab
- Mercedes Materials Testing Lab
- Mercedes Standards Testing
- Mitsubishi Standards Testing
- Nissan Standards Testing
- PV 3900 VW Odor Test
- SAE Specs
- Subaru Standards Testing
- Tesla Standards Testing
- TL 211 Automotive Testing
- TL 226 Testing
- TL 527 Testing
- TL 528 Testing
- TL 52388 Testing
- TL 52722 Testing
- Toyota Parts Testing
- Toyota Standards Testing
- Toyota VOC Testing
- VDA 230-219 Testing
- VDA 270 BMW Odor Test
- Volkswagen Approved Lab
- Volkswagen Approved Testing Lab
- Volkswagen Parts Testing
- Volkswagen Standards Testing
- Volkswagen VOC Testing
- Volvo Standards Testing
- VW 44045 Testing
- VW Approved Test Lab
- VW Approved Testing Lab
- VW Validation Testing