- Home
- Services/IndustriesServicesindustries
- About Us
- LocationsStatesAccordion ContentAccordion ContentAccordion ContentAccordion Content
- Job Openings
- Quick Links
- ATS Family
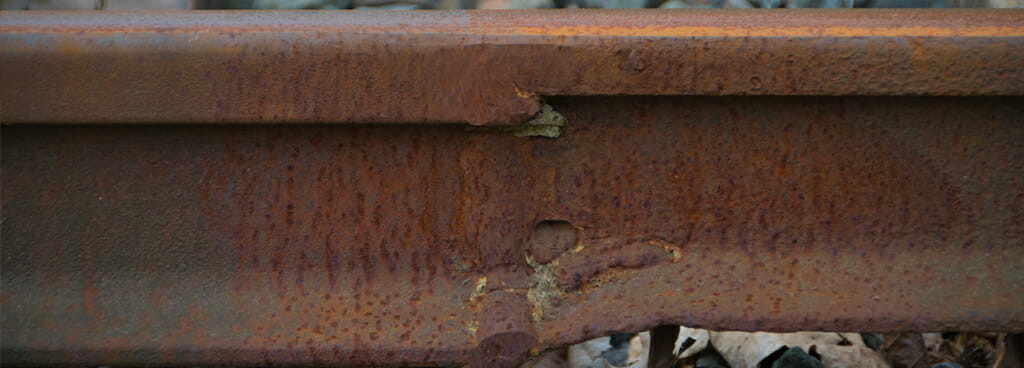
Ultrasonic Rail Testing Services
The Applied Technical Services (ATS) NDT Division offers ultrasonic rail testing. Our experts are SNT-TC-1A Certified Technicians offering thorough inspections to reduce the risk of rail failures —the second leading cause of railway accidents behind railcar defects. Rail failures can be caused by manufacturing defects, abnormal traffic effects, rail corrosion, poorly maintained joints, or improper welding. ATS provides ultrasonic rail testing solutions nationally and internationally to a variety of clients in the rail industry.
Types of Rails Inspected:
- Class 1 Railroads
- Commuter Rail
- Light Rail
- Monorails
- People Movers
- Ports
- Short Line
- Streetcar
- Trolley
Ultrasonic Testing
Ultrasonic testing is the most popular NDT method used on rails today. ATS offers traditional ultrasonic testing and phased array ultrasonic rail testing. This method is ideal for rail inspections since it can detect surface and subsurface fatigue fractures, material deformations, and weld discontinuities through ultrasound technology. It is applicable to most parts of the rail including rail heads, rail footers, and rail welds.
Common Defects Revealed Through Ultrasonic Rail Testing:
- Horizontal Cracks in Head
- Vertical-longitudinal Slit in Head
- Horizontal Crack at Web Foot Junction
- Horizontal Crack at Head Web Junction
- Bolt Hole Crack
- Transverse Fracture
- Transverse Fatigue Crack in Head
- Horizontal Crack at Stop and Bottom Fillet Radius
- Vertical – Longitudinal Crack in Foot
- Transverse Cracks in Rail Foot
- Lack of Fusion, Cracks, Porosity, Slag Inclusion in Welds
Thermite welds can be one of the most problematic regions of a rail system, making routine inspections imperative. Our experienced technicians are familiar with rail industry standards and codes. Our experts arrive on time, equipped with the proper tools, training, and experience to ensure accurate readings. We provide instant results and detailed reporting of weld inspection findings.
Additional Rail Testing Services
ATS provides comprehensive lab services beyond our field rail inspection capabilities. If you need to validate a manufacturing process or confirm quality assurance, our A2LA Accredited labs offer a wide variety of materials testing and chemical analysis services. In the non-destructive field, traditional and digital x-ray can reveal defects in the completed weld. As for destructive testing methods, out technicians can use metallography techniques to show the nature of potential defects in more detail.
Chemical Analysis — We offer a range of analytical chemical analysis techniques to confirm the alloy of rails and welds, including Optical Emission Spectroscopy (OES) analysis, Inductively Coupled Plasma (ICP), and Wavelength Dispersive X-ray Fluorescence (WD-XRF).
Weld Hardness Testing — ATS performs both Brinell Hardness Testing per ASTM E10 and Rockwell Hardness Testing per ASTM E18. Either of these methods may be used to investigate the hardness of both weld and base metals, depending on the required standards.
Metallography Tests — Our labs have the technology to perform micro- and macro-structural analysis of these welded rails in cross section. This analysis can reveal welding porosity, incomplete fusion, microstructural characteristics, and micro-indentation hardness variations across both the weld and base metals.
Internal and Surface Hardness Testing — Micro-indentation hardness testing per ASTM E92 or E384 can be conducted on weld cross sections to investigate any variations in hardness produced during the welding process from the weld metal to the heat affected zone (HAZ) to the base material. These tests can be conducted on various Vickers or Knoop hardness scales at ATS, per applicable requirements.
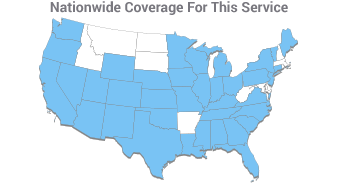
Request Form
"*" indicates required fields
NDI Inspections
- Flow-Accelerated Corrosion Testing
- Hull Inspections
- Industrial Heat Treating
- Metal X-Ray Testing
- NDI Companies
- NDI Eddy Current Inspection
- NDI Laboratory
- NDI Liquid Penetrant Testing
- NDI Magnetic Particle Testing
- NDI Specialists
- NDI Test
- NDI Radiography Testing
- NDI Ultrasonic Testing
- NDT Welding Inspection
- Nondestructive Inspection