- Home
- Services/IndustriesServicesindustries
- About Us
- LocationsStatesAccordion ContentAccordion ContentAccordion ContentAccordion Content
- Job Openings
- Quick Links
- ATS Family
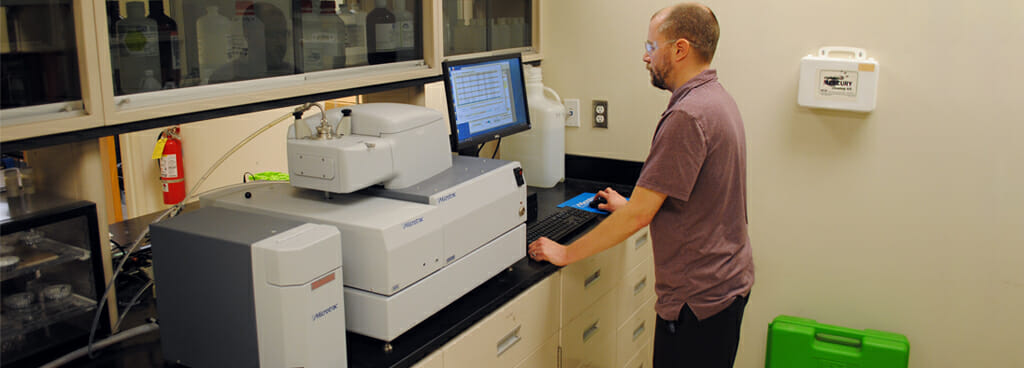
The Importance of Powder Characterization
Applied Technical Services offers powder characterization to help manufacturers ensure their design materials meet their requirements. Our chemical analysis division can analyze a powder sample to determine a wide variety of attributes important to a final product’s performance in a service setting.
Everything about a powder needs verifying before it can see widespread use in a final product. For example, if the particles in a toner ink cartridge do not fall within a certain size range or differ wildly in shape and uniformity, the printed page’s image quality becomes much poorer. Alternatively, if materials suppliers send a grade of steel powder other than the one identified in the product specifications for an additively manufactured component, that piece’s physical durability may be compromised.
Manufacturers send powder samples to third-party testing labs like ATS to avoid the sorts of problems outlined above. ATS’ chemical analysis labs perform all powder characterization services. These specialists select the most appropriate techniques from a variety of testing methods to identify the material composition and define the size and shape of client samples.
Material Identification
When designing a new product, engineers select each material for its distinct qualities —tensile strength, impact durability, electrical conductivity, high melting point, elasticity, corrosion resistance, or whatever else may appeal — because of how it can contribute to the success of the final assembly in expected service conditions. One guaranteed way of not getting a design material’s desired benefits is to use the wrong one, whether due to a mix-up with a vendor or contamination in the powder production process. We help clients verify the identity of their powders using the following methods:
Primarily used to identify polymer samples and pharmaceutical powders, this method allows ATS chemists to determine the identity of the polymer or rubber material. The method works by comparing the characteristic spectra emitted by analytes exposed to infrared waves against a comprehensive library of references. Our lab maintains ISO 17025 accreditation through the A2LA to perform this method to ASTM E1252.
When presented with a metal sample, our chemists opt for this method instead. By first using an acid to digest the sample into a liquid, atomizing the liquid and then exciting it via introduction to a plasma, our equipment can identify its elemental composition and measure each element’s presence down to the low parts-per-million (ppm) range. We maintain A2LA accreditation to perform this method to ASTM E1479 and E1613.
Finally, a sample contaminated through ineffective processing can lead our chemists to employ SEM/EDS instead. Shooting the analyte with a beam of high-powered electrons causes the surface of the specimen to emit a spectrum of characteristic X-rays, which an X-ray detector picks up and processes to determine the approximate elemental makeup of individual particles. SEM/EDS testing also allows for high magnification imaging and dimensional measurement of individual particles. We maintain A2LA accreditation to perform this method to ASTM E1508.
Measurement and Morphology
Another aspect that can determine the effectiveness of a given powder is the size and shape of its particles. Particles with wildly different sizes and shapes do not settle as evenly along a surface as those with a more consistently spherical form and narrow size distribution. These attributes can negatively affect the performance characteristics of the final product — ranging from low impact durability in an injection-molded component to insufficient scratch resistance for a powder coating. Irregular particles may arise from flawed processes when creating their powder from base materials. We help clients validate their processes by measuring the particle size distribution and particle morphology.
Light Scattering / Laser Diffraction
ATS chemists use Light Scattering (also known as Laser Diffraction) to take a simple measurement of the particles in a powder sample. Our particle analyzer cycles the specimen through the path of a laser beam. By recording the angle and intensity of the light scattered when it hits a given particle, the equipment’s processor can apply an algorithm to calculate the diameter of that particle. Performing this process several thousand times in seconds yields data that our powder characterization specialists can use to determine the range of sizes present in the sample, called the particle size distribution. Our chemists conduct this method to ASTM D4464, ASTM B822, and ISO 13320.
Dynamic Image Analysis (DIA)
For a more comprehensive assessment, our chemists use Dynamic Image Analysis (DIA) to measure the shapes of particles in a powder sample. This method allows them to describe the shape of particles using twenty-six different dimensions. Our equipment cycles analytes in front of a camera that takes and collates thousands of shots capturing the particles from all different orientations. Doing so allows the analyzer to calculate the values associated with individual particles’ dimensions, reducing the margin of error compared to other methods.
About Applied Technical Services
Applied Technical Services has provided clients with our testing, inspections, and consulting engineering capabilities since our founding in 1967. The past 50+ years have allowed our company to grow vastly. Far from the three engineers aiding local businesses out of our founder’s basement, we now represent a multidisciplinary firm that serves clients operating around the world through the efforts of 1,000+ chemists, inspectors, calibrators, scientists, Professional Engineers, technicians, investigators, and trainers. The industries that most benefit from our powder characterization expertise and comprehensive capabilities include:
- Additive Manufacturing
- Powder Metallurgy
- Renewable Energy
- Power Generation
- Oil / Gas
- Manufacturing
- Healthcare / Medical
- Nuclear
- Chemical
- Construction
- Defense / Military
- Communications
- Aerospace
If your company needs powder characterization services from a trusted provider, contact ATS today for a free quote — We take a closer look!
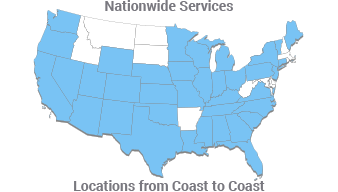
Request Form
"*" indicates required fields
Chemical Analysis
- Ash Testing
- Azo Dyes
- Azo Dye Testing
- Benzene Analysis
- Biocompatibility Testing for Medical Devices ISO 10993
- Chemical Composition Testing Lab
- Cleanliness Testing Lab
- Contamination Test
- Combustion Analysis
- CPSIA Testing Lab
- DSC Analysis
- DSC Analysis of Polymers
- DSC Polymer Characterization Analysis
- DSC Testing
- Ethylene Oxide GC MS Analysis
- EPA Method 24 Testing
- Extractables Leachables Testing
- Extractables Testing
- Flame Retardant Chemicals
- Formaldehyde Testing
- FTIR Analysis
- FTIR Chemical Analysis
- FT-IR Material Analysis
- FTIR Surface Analysis
- FTIR Testing
- Gas Chromatography Mass Spectrometer Analysis
- GCMS Analysis and Testing
- GCMS Oil Analysis
- Halide Anion Testing
- HPLC Analysis Services
- ICP-AES Analysis
- ICP-OES Testing
- ION Chromatography Testing
- ISO 10993 Testing
- ISO 10993 Testing Lab
- Karl Fischer Testing
- Leachable Testing
- LECO Testing
- Melting Point Analysis
- Methane Analysis Gas Chromatography
- Methanol Contamination Testing
- OES Materials Testing
- Optical Emission Spectroscopy
- PAH Testing
- Particle Size Distribution Analysis
- Particle Size Distribution Analysis Laboratory
- Particle Size Distribution Testing
- PFOA Testing
- PFOS/PFOA Testing
- Plastic Impact Testing
- Plastic Pipe Testing
- Polymer Characterization Lab
- Polymer Material Testing
- Polymer Testing and Analysis
- Powder Characterization
- Product Formulation
- Solvent Testing Lab
- TGA Analysis
- TGA DSC Analysis Lab
- TGA Moisture Analysis
- TGA Polymer Testing
- Thermal Analysis Services
- UV VIS Testing
- VDA 19.1 Cleanliness Testing Lab
- Ventilator Component Cleanliness Testing